Skip to content
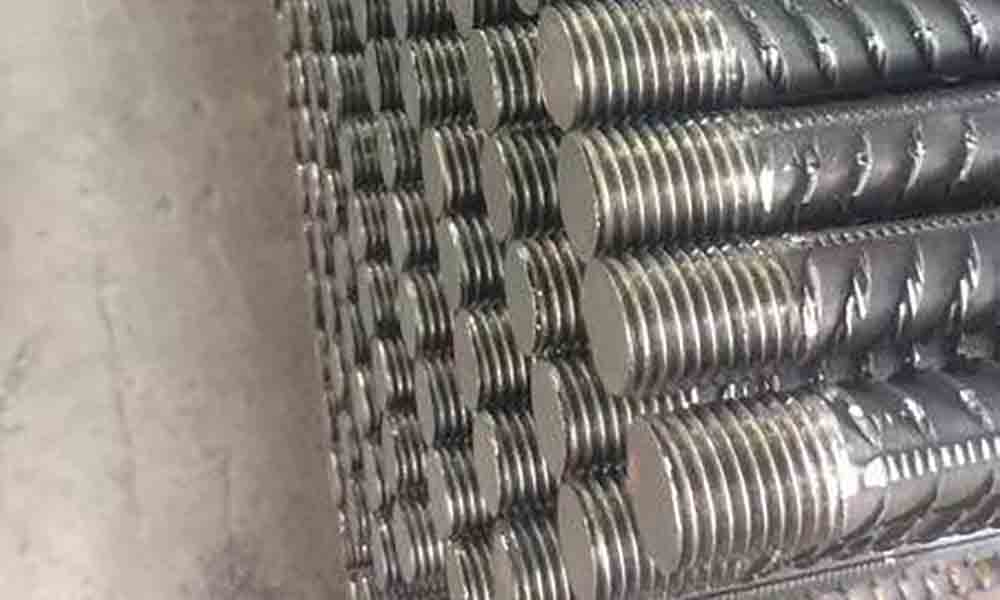
Steel Bar Threading Machine Pre-Operation Checks
- Steel Bar Threading Machine Electrical Inspection:
- Inspect electrical parts for any damage.
- Ensure the machine body is properly grounded.
- Power Supply Verification:
- Confirm that the power supply voltage matches the machine’s working voltage.
- Ensure the distribution box is located within 3 meters of the motor.
- Safety Components:
- Verify that the machine is installed smoothly with complete and reliable safety protection components.
Initial Setup
- Idle Test:
- Run the machine without load to test both the forward and reverse functions of the motor.
- Ensure that the machine and the water pump are functioning correctly.
Preparing Steel Bars
- Selection:
- Choose steel bars that exhibit good longitudinal linearity.
- Ensure the cut end face is perpendicular to the steel bar’s axis. If not, cut and polish the end face before threading.
Loading Steel Bars
- Teamwork for Lifting:
- With the assistance of another person, lift the steel bar onto the workbench.
- Clamp it securely and adjust for concentricity to prevent loosening and potential injuries.
Threading Process
- Starting the Threading:
- Begin threading slowly, gradually increasing speed while maintaining a uniform threading speed.
- Ensure that the thread teeth remain intact to prevent equipment damage.
Handling Semi-Finished Products
- Lifting:
- After processing the first thread, use the help of another person to lift it onto the semi-finished material rack.
- Connect and lock it using the appropriate sleeve, ensuring proper locking and threading quality by observing and feeling for tightness.
Quality Inspection
- Sampling:
- Sample threaded connectors under the supervision of a witness and send them to the laboratory for quality inspection.
- If the laboratory inspection passes, continue processing threaded joints of the same specification.
Troubleshooting
- Immediate Actions:
- If the machine operates poorly or the knife gets stuck, stop the machine immediately for inspection and repair.
- Debris Cleaning: Do not clean debris from the blade while the machine is operating.
Safety Measures
- Personal Protective Equipment:
- Operators must wear goggles.
- Avoid touching rotating parts while wearing gloves.
Post-Processing Care
- Cleaning and Protection:
- Clean the processed threaded interface and protect it from rain and corrosion.
- Ensure the coolant is clean and free of impurities; replace it monthly.
- Add and replace gear oil in the reducer every three months.
Maintenance
- Regulatory Compliance:
- Perform maintenance and repair on the machine according to established regulations.
End of Operation
- Power Down Procedures:
- Turn off the power and lock the distribution box.
- Clean the work area before leaving.
Rebar Threading Machine
Steel Bar Threading Machine Standard Sleeve Geometric Dimension
Specifications |
Sleeve Length (mm) |
Thread Length (mm) |
Thread Number |
Pitch (mm) |
16 |
45 |
22.5 |
9 |
2.5 |
18 |
55 |
27.5 |
11 |
2.5 |
20 |
60 |
30 |
12 |
2.5 |
22 |
65 |
32.5 |
13 |
2.5 |
25 |
70 |
35 |
12 |
3.0 |
28 |
80 |
40 |
13 |
3.0 |
32 |
90 |
45 |
15 |
3.0 |
Minimum Tightening Torque for Straight Thread Joint Installation
Rebar Diameter (mm) |
Tightening Torque (N·mm) |
≤16 |
100 |
18–20 |
200 |
22–25 |
260 |
28–32 |
320 |
36–40 |
360 |
50 |
460 |